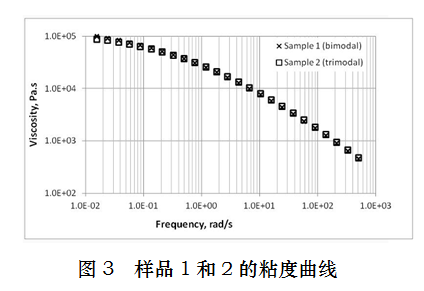
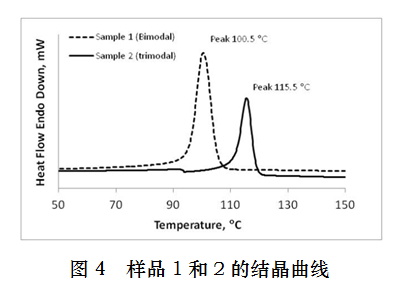
2.2 收缩性 BNT成核形成了更好的晶体结构,如图5所示。更好的晶体结构导致收缩行为不受色母粒影响。如图6所示,非成核样品收缩率在1.27%至1.77%之间,它取决于所使用的色母粒。而BNT成核样品的收缩率一致(1.8%),不取决于色母粒。这使得在管材挤出和管件注塑时颜色变化更快,不需要调整加工条件。
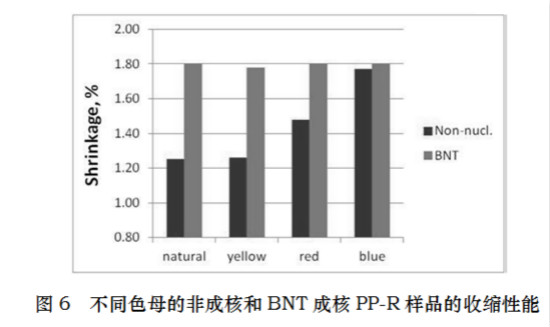
2.3 均匀性
正如本文前面所讨论的,由于聚合物重叠部分,三峰分子量分布改善了材料均匀性和色母粒的分散性。改善的均匀性和色母料分散性在显微照片中清晰可见,如图7所示。三峰样品2(图7a),显示了色母粒在基材中的分布非常均匀。然而双峰样品1显示了明显较差的均匀性,而且在显微照片(图7b和c)中能看到明显的污点。 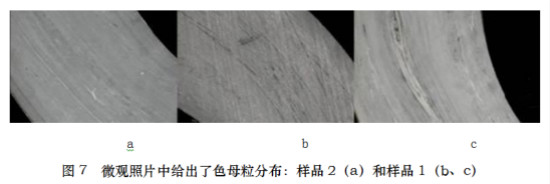
2.4 管材挤出 本文对样品1和2的全尺寸范围内加工性能进行比较。挤出机和管线设置在表2中进行了总结。生产了三种不同管径的管材:32mm,63mm和110mm。试验中螺杆速度设置为170rpm,测量熔体温度约为220℃,如上文所述,样品1和样品2的流变行为相似,因此他们的加工性能是可比较的。这一点在试验中被证实,如表2中所示。在管材挤出过程中仅看到熔压和产量有轻微的不同,两种原料挤出的管材都具有良好的表观质量。 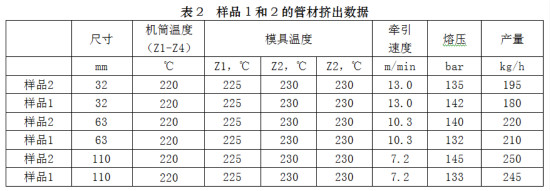
试验人员期望能够从BNT成核原料的管材挤出中得到额外收益。由于BNT成核材料较高的结晶温度,可以在不需要增加额外冷却能力的情况下提高管材挤出线速。这样能够得到较高产量,同时保持良好的最终产品尺寸稳定性。 2.5 管件的注塑 图8中概述了管件注塑的流程步骤。由于BNT成核样品2的结晶温度较高,如上文所述,可以明显减少控制和冷却时间,从而使这个周期时间缩短20%以上,因此得到比传统PPR牌号高出20%的生产率。 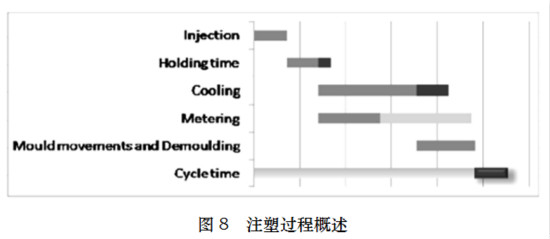 除了缩短生产周期以外,相对于不成核样品1来说,BNT成核样品2提高了管件尺寸的稳定性。表3对比了不同类型注塑管件的椭圆度,还给出了冷却时间的影响。椭圆度的测量结果证明样品2显著提高了尺寸稳定性,不受冷却时间和产品尺寸的影响。样品1的椭圆度变化范围是0.4mm到0.9mm,取决于最终产品尺寸和冷却时间,而样品2无论最终产品和冷却时间如何,都表现出了优异的尺寸稳定性。 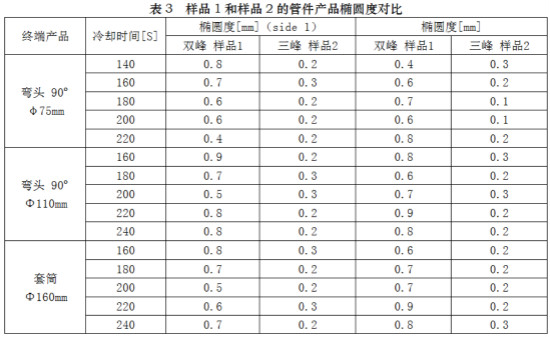
3 结论 ·三峰PP-R可以改善聚合物结构调整,显著的提高冲击性能而且对模量没有负面影响。这就产生了独一无二的刚性-韧性平衡,这种平衡是单峰和双峰PP-R牌号都无法达到的。 ·可以通过优化三峰PP-R牌号的流变行为来确保全尺寸管材产品具有优良的加工性能。 ·由于重叠的Mw部分,相对于双峰PP-R原料,三峰PP-R原料表现出了更好的色母粒分散性和均匀性。 ·BNT成核技术将PPR牌号的结晶温度升高了15℃,得到了更好的晶体结构。这使BNT成核材料收缩性能稳定,不受所用色母粒的影响,使得管材挤出和管件注塑过程中产生更快的颜色变化。 上一页 [1] [2] [3] 下一页 |