应用于油气田基础设施中的 聚乙烯管材的使用寿命评估 约翰内斯开普勒大学聚合物材料与测试学院 R. W. Lang, P. F. Schoeffl
摘要:近年来,一些企业对在油田工程领域采用PE-HD管道(如注水管、排水管)很感兴趣,为满足这一需求,我们已建立了一个全面和完整的综合测试方法用于评估外力作用下承压管道的使用寿命。在这一方法中,我们设计并采用了专用的实验技术和测试流程,在外力作用条件下采用室内试验(拉伸和断裂力学测试)及组合件试验(承压管道测试)表征材料性能,本方法涵盖了所有相关管道破坏形式(三个失效的主要区域,区域I-III)[1-3]的破坏测量和分析,因而,在典型的油田使用要求和环境条件下,对管道使用寿命的预测最长可达25年。本文选用PE100与PEXc作为模型材料。外力条件试验在液态烃(LHC;90/10 W-%异辛烷/甲苯)中进行,试验温度分别为35℃及60℃,并以去离子水作为参照环境。与在去离子水中进行的试验结果相比,管材在LHC中进行液压试验(包含10000 h测试时间的结果)时,长期静液压强度(LTHS)下降了约50%。关于材料SCG行为方面的变化,缺口圆棒试样循环测试结果表明(CRB;在介质完成浸没下进行107次以上失效循环),在低应力强度因子(SIF)的LHC溶液中进行饱和处理后,试样的抗SCG性能比在水中更佳。此外,在水中进行的CRD试验结果表明缺口尖端开裂是导致材料破坏的主要原因,而在LHC饱和溶液中进行的缺口圆棒试样试验中观察到的破坏模式为循环剪切屈服。考虑到材料的老化与降解,我们进行了两年的长期暴露试验,然后测试样品的氧化起始温度(Tox),并辅以体积排阻色谱法(SEC)对聚合物分子质量分布变化进行测定。因此,对用于油田压力管道的现行PE管材分级材料,本文首次提出了对其结构性能进行综合评估的数据。
1 引言 一般通过管材材料自身特性(特别是静液压试验、耐慢速裂纹增长和耐快速裂纹扩展)和环境条件(如介质和温度)对管材内部和外部产生的叠加应力,对特定用途的塑料压力管道使用寿命进行评估。在这些特性中,通过压力试验得到的管材长期静液压强度(LTHS)对管材使用寿命评估最重要,也是现有管材寿命评估的主要方法 [4,5]。由于内压(管材在环向和轴向可自由移动条件下)在管壁上产生三个方向的应力,并最终导致管材破坏。在实验室条件下,导致承压管道破坏(破裂)的原因除了应力之外,还取决于试验条件(如加压介质、温度和外部环境)。PE压力管材寿命曲线可以分为三个区域,每个区域对应一种破坏机理。表现为大尺寸屈服变形的韧性破坏(I区),慢速裂纹增长(SCG)引发的准脆性破坏(II区),材料大量降解引起的脆性破坏(III区)。长期静液压强度几乎完全与I区相关,它是用来表征几十年内管材耐静液压的能力,通常是按标准管材材质分级规范(主要是ISO 9080和ASTM D2837)进行水压测试获得。在严苛的环境条件下(增塑剂的作用或增强化学老化),必须考虑到材料“弱化”的问题,一般采用使用系数以降低在水中测定的长期静液压强度值,确保使用安全[6-12]。 目前对这项工作主要是采用、修正和扩展以水为介质对聚乙烯(PE)管材使用寿命进行评估的试验方法,转而使用液烃和以应用为重点的其它严苛环境条件下的试验方法(例如叠加外力和环境条件,代表应用环境的试验介质)。在严苛的环境介质条件下,由于附加的物理(吸附、浸出)和化学(高聚物和稳定剂的降解)作用,材料的破坏机理与在水中明显不同。因而,在此条件下,综合考虑了多种影响因素的更加全面的试验方法(“整体测试理论”)更为适合。为了获得模拟实际应用条件下的试验数据,在本项研究中提出了一种包括试验装置及测试过程的试验方法,在此方法中通过特制的试验装置,如可对样品进行试验的介质密封容器,可采用LHC对管道组合件进行压力试验的装置,可对I区、II区和III区所对应的破坏机理进行研究。此外,本方法中还采用色谱及热分析方法,在分子水平分析了溶剂对材料的影响。笔者也明确指出,对于本文中没有提及的渗透问题应进一步研究。本项研究的目的在于为合理设计管道力学结构提供足够的信息。
2 方案与试验 2.1管材使用寿命的全面评估(整体测试理论) 下文描述了传统试验方法的测试流程,但在一定程度上扩展到严苛介质环境条件下材料性能测试。如图1所示,采用整体测试理论进行试验(包括特定环境条件测试装置的开发),包括所有三个破坏机理的分析(I区到III区)。此测试的目的是在叠加外力作用条件下,表征在实际使用环境下管道材料的性能。为说明可能导致PE管道破坏的不同机理,整体测试理论将测试分为实验室样品测试、管材或管道组合件测试及分子测试。 · 相对于组合件测试,小尺寸试样测试可在相对很短的时间内,在叠加外力环境条件下(与管材的具体应用环境有关)表征材料的基本性能。同时也对估计管材测试(I区)时应采用的应力水平十分有用。采用实验室样品测试所确定的材料耐慢速裂纹增长性能同样重要,因为这可以表征不同等级的材料在特定液体介质中韧性-准脆性破坏转变(拐点)。 · 通过在严苛液体介质条件下对管道加压的方式进行的组合件测试是管道使用寿命评估的核心部分,主要原因是长期静液压强度(LTHS)值对确定管网中所用管道的规格至关重要。 ·通过一系列方法对分子降解、稳定剂保留率及其他老化因素的影响进行了分析。
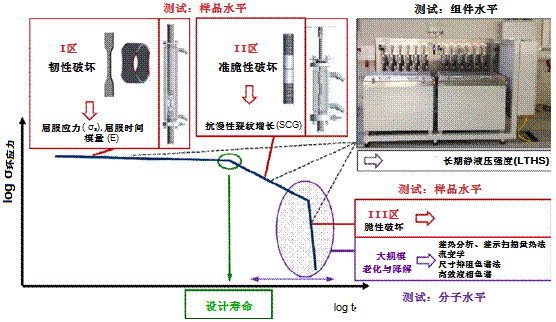
图1 在苛刻的环境条件下用于PE压力管材寿命评估的整体测试理论的示意图
2.2 液态环境与样品预处理 本研究所用的液体介质是根据油田所用PE压力管道的要求来确定的,而这些管道要与很多不同的液态碳氢化合物(LHC)接触。为了模拟管道材料直接接触油气冷凝物的“最坏条件”,我们选定重量比为90/10的异辛烷/甲苯的混合物做为LHC参照环境。此外,采用去离子水作为注水管的参照环境及一般参照环境。 对于实验室样品测试而言,在进行单一/静态测试或循环测试试验之前,所有在LHC环境下测试的样品应首先在相应的环境条件及指定的力学测试温度下进行预处理(浸没),直至饱和(质量恒定)。去离子水环境中进行测试所用的ISO 5A试样应在指定试验温度下在去离子水中进行预处理,因PE材料几乎不吸水,处理时间只需2h。组合件测试时,管材样品应在其内部充满相应的测试液体并用氟橡胶插头密封后放置于指定试验温度的加热炉中至少4周,在大气压下达到质量恒定。采用去离子水进行压力试验的样品不需进行预处理。为了在分子水平上进一步表征聚合物,ISO 5A试样分别在35℃和60℃下,在去离子水和90/10异辛烷/甲苯溶液中浸渍多个时间段(30、90、180、360和720天)。然后通过差热分析(DTA;通过氧化起始温度确定稳定剂保留率)和体积排除色谱法(SEC;分子降解)进行研究。 2.3 测试装置和设备 对单一/静态测试类型的ZwickRoell Z005型的螺杆驱动万能试验机(Zwick GmbH & Co. KG, Ulm,D)和针对循环测试英斯特朗E3000型的电动测试系统(Instron,Norwood,MA/USA)配备了环境控制单元,笔者的其它文章中对此进行了详细描述[1,3]。标准试验方法中通常采用水压试验表征材料性能,以此为基础,本研究设计并采用了可在不同温度下以各种严苛液体如液烃和乙二醇为介质,并可精确控制内压的压力试验设备[2]。氧化起始时间是通过DSC 4000(Perkin Elmer,Waltham MA/USA)进行测定的。SEC实验则委托北欧化工聚烯烃有限公司(奥地利林茨)进行测定。
3 结果与讨论 3.1 I区破坏机理(长期静液压强度;LTHS) 第一组ISO 5A试样在空气中或LHC环境中测试,以研究经过LHC预处理的试样单调应力-应变行为的差别。测试温度为60℃,应变速率为10-3•s-1(饱和预处理条件下,LHC吸收量约7.5%(重量分数))。作为参照,未经预处理的试样也在空气中进行测试,其它试验参数与经过预处理的试样相同。试验结果如图2所示,为公称应力(工程)与公称应变(由夹持长度和横梁位移确定)曲线。正如我们预期的那样,由于被吸收的LHC的增塑作用,未经预处理试样的屈服应力约11.7MP,而经过预处理试样的屈服应力约7.7MPa,下降了约35%。值得注意的是,对经过预处理的试样在空气中或在LHC环境中进行测试时,在两种条件下测得的试样的应力-应变曲线在屈服后变形区发生明显分离,在公称应变相同时,LHC环境下测试的样品的应力较低,这与LHC环境下测试的试样在屈服后变形区吸收了更多的LHC有关[3]。
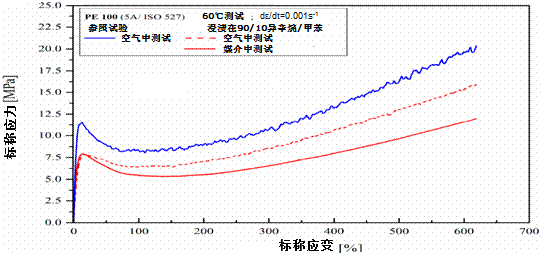
图2 PE100-2标称应力/应变关系曲线 (经过预处理的5A试样在LHC中或空气中测试比较,未经预处理的试样在空气中测试作为参照)
图3为PE100管材的水压试验和液烃压力试验的破坏时间与环应力的对数关系曲线,这个测试一般用于确定管道在特定条件下(应力(σ),温度(T)和时间(t))的长期静液压强度(LTHS),也可按公式2所述(C1、C2、C4三个参数模型),通过ISO 9080规定的标准外推法(SEM)预测输水用管道的使用寿命。在LHC环境下管道压力试验曲线上可以看出,过渡阶段发生在试验进行100h左右,(以空心符号表示),这与特定试验参数(温度和压力)下达到吸附平衡的时间及相应的高聚物材料自由体积变化有关。因此,100h以内得到的LHC压力试验结果在外推公式中不采用。试验曲线上100h以后的测试结果所显示的线性破坏行为与水压试验曲线几乎平行,但时间相同时,环应力明显较低,在35℃和60℃时,LTHS均下降约50%。此外,图3中包含两个独立的测试实验室在60℃下以水加压管材测试结果,即在本研究中所描述的设备所得结果(参照IPMT)和北欧化工聚烯烃公司(奥利地林茨)在提供相同的材料等级的测试结果(在Exova(瑞典斯图斯维克)进行测试)。我们发现这两个试验所得结果具有很好的一致性。用Pipeson分析软件(瑞典斯德哥尔摩)将Exova得到的60℃和20℃下的试验数据插入在35℃下的水压测试结果(图3中的蓝色虚线)。

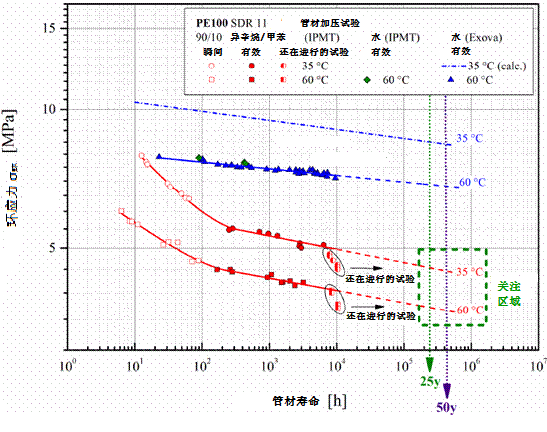
图3 在水和液体烃类加压测试的PE100环应力曲线 (水中测试的数据(蓝色符号)由北欧化工提供)
图4给出了另一种材料等级(PEXc)在液态烃加压测试中相应的环应力水平所对应的失效时间。在水中测试的参照曲线由Exova(由北欧化工聚烯烃有限公司提供)测试数据经PIPESON分析软件计算得出。所取得的数据利用SEM进行再推算以获得长期静液压强度的数据,由于液烃的增塑作用,得出通过液态烃加压测试的LTHS总体下降约50%。相同材料等级,PEXc的长期经液压强度明显高于PE(在水中测试结果高约10%,在液烃中测试结果高约20%)。
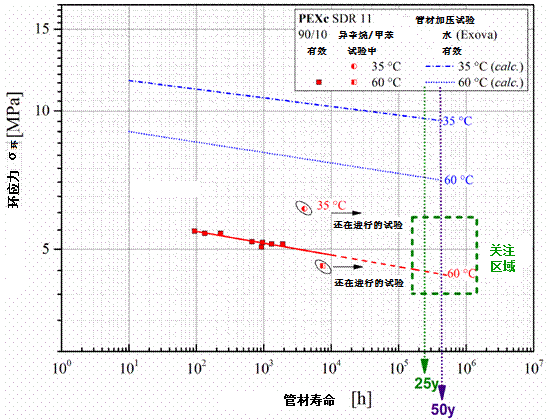
图4 PEXc管材在一定的加压介质,压力和温度下环应力曲线 (箭头表示还在进行的测试)
3.2 II区破坏机理(耐慢速裂纹增长;SCG) 图5给出了在35℃下,PE100的CRB样品分别在水中和90/10异辛烷/甲苯中的循环破坏行为曲线。将初始循环应力强度因子范围ΔKI,in(f =10Hz,R =0.1)与破坏时间的关系绘制曲线。考虑到“blunt”裂缝的增长,显然应将ΔKI,in作为为Y轴参数。在水中的测试破坏曲线给出一个越来越明显的拐点,说明了材料从主要韧性破坏(称为I型破坏)过渡到尖锐裂纹稳定增长导致准脆性破坏(II型-SC)。相较于水中实验,在LHC环境测试的破坏曲线在开始阶段ΔKI值较低。对于后者,观察到的破坏主要是由“blunt”裂纹增长引起的(II型-bc,裂纹末端剪切屈服机理),破坏曲线斜率明显低于在水中产生的II型-sc破坏(裂纹尖端开裂机理)。最值得注意的是,测试时间为100h时(3.7×106次循环),在90/10异辛烷/甲苯和水中测得的使用寿命数据有一个交叉点,在交叉点之后,LHC环境下测试的时间-破坏曲线高于在在水中的时间-破坏曲线。进一步的试验结果、试验方法和数据处理的细节及试验现象解释详见笔者其它文章 [13-15]。 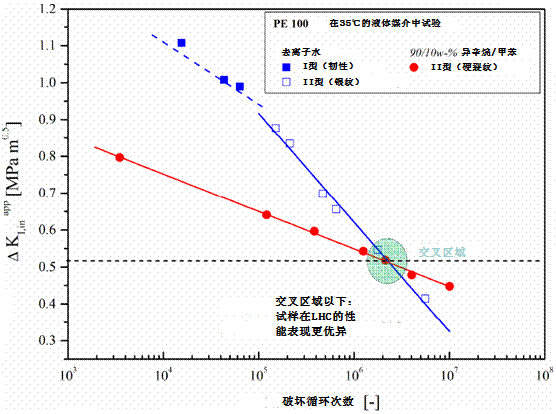
图5 PE100模型材料35℃时在水中和LHC环境的循环CRB测试
3.3 III区破坏机理(大规模老化及材料降解) 作为这项研究的一个例子,PE100试样浸入60℃的90/10异辛烷/甲苯保持30天,然后用体积排阻色谱法分析。如图6所示,浸渍90/10异辛烷/甲苯后,分子量分布曲线在很大程度上仍与基准曲线一致(未浸渍的材料),但我们发现低分子量质量组分有轻微地减少(可能与低分子量石蜡基馏分有关)。为了更好地反映长期运行条件,包括对更长期的老化浸渍样品进行SEC分析的进一步的测试工作正在进行,试验结果另行发布[3]。如图7所示,分别浸在去离子水和90/10异辛烷甲苯720天(> 17000h)的PE100样品的氧化起始温度(Tox),分别与未加稳定剂/未浸泡的参照样品(205℃)和添加稳定剂/未浸泡的参照样品(265℃)比较。在60℃和35℃的去离子水中浸泡720天后,试样的Tox值从265℃分别下降到240℃和253℃。相对于浸渍在去离子水中的样品,浸渍在90/10异辛烷/甲苯中的试样,Tox值在浸渍的前30天出现下降。正如预期,相对于30℃(Tox = 248℃),在60℃(Tox = 230℃)下降更为明显。虽然我们不清楚稳定剂浸出占稳定剂消耗总量的确切比例,但很可能由于90/10异辛烷/甲苯促进了试样中稳定剂的析出,导致试样Tox值明显下降。此前的研究结果表明,试样在水中浸渍稳定剂也会有微量滤出[16,17]。后续试验中,在60℃浸渍720天的试样的Tox值下降至220℃,35℃浸渍的试样的Tox值下降至226℃,前者比后者略低。
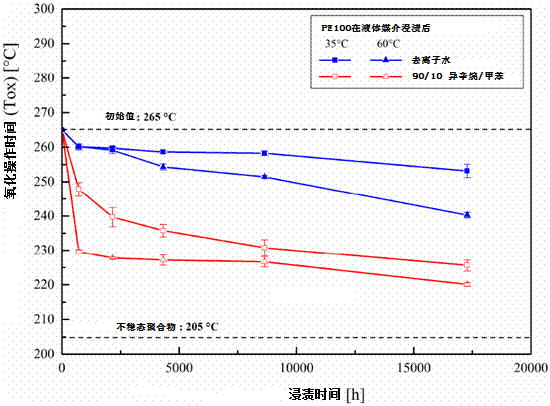 图6 在90/10异辛烷/甲苯研究浸渍后 图7 PE100浸没在水和90/10异辛烷 观测PE100的体积排除色谱分析 /甲苯后的氧化起始温度
4 结论 研究结果表明,PE100和PEXc材料在以液烃为介质的静液压试验中测得的数据与在水中测得的数据相比,管道的长期静液压强度(LTHS)下降了50%。如图8所示,在应力较低时(与管道实际应用时LTHS值的降低一致),PE100在LHC环境中耐SCG性能降低,但优于在水中的耐SCG性能。此外,根据ISO 9080标准外推法进行的水压试验中,在50年内PE100材料没有明显的拐点,因此推断SCG应不会成为PE管道在油田应用时使用寿命达到25年的瓶颈。 尽管本文中采用高温液烃代表管道实际应用时可能面临的最坏情况(液烃分子直径小,与PE有很好的亲和力及很高的分子流动性),但浸渍2年后,试样的Tox值仍明显高于与未加入稳定剂的参照试样。这与作者此前的研究成果相符[18],即在经过15年的使用后,油田用PE管材的Tox值仍明显高于未加稳定剂的高分子材料。一般来说,氧化起始温度和分子量分布是表征使用中的PE管材材料老化状态的重要参数(稳定剂消耗量和材料降解)。因而,根据上述整体测试理论,笔者建议在严苛介质条件下如油气(凝析油)使用的管道,应在规定的时间范围内进行监控。笔者也明确指出本文中未讨论渗透的问题,应做进一步研究。本项工作的目的在力学和老化性能方面为管道设计提供足够的信息。
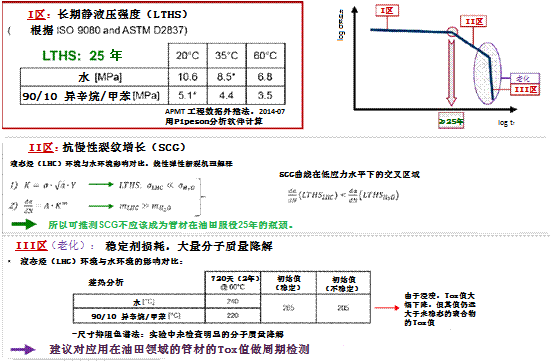
图8 基于引进的“整体测试理论”所得结果 对在油田环境服役PE100级管材的使用寿命进行评估
参考文献 [1] P.F. Schoeffl,P.Bradler,R.W. Lang,叠加力学环境负荷下的聚合物在苛刻的液体介质条件下—— I. 屈服和裂纹增长行为的表征,文章即将发表. [2] P.F. Schoeffl, H.Schobermayr, R.W. Lang, 叠加力学环境负荷下的聚合物在苛刻的液体介质条件下—— II. 长期静液压强度(LTHS)的测定,文章即将发表. [3] P.F. Schoeffl, 正在进行的博士论文, Johannes Kepler University, Linz. [4] K. Richard,E. Gaube,G. Diedrich,Kunststoffe,1959,49,516. [5] ISO 9080: 塑料管道系统-通过管道外推形式测定热塑性材料的长期静液压强度. [6] J. Hessel,E. Barth,B. Kempe,Mater Corros,1997,48,273. [7] U. Andersson,M. Ifwarson,Plastic Pipes X. 会议,1998,哥德堡/瑞典. [8] API 15LE: 聚乙烯(PE)管线规范. [9] ISO 4437: 燃气用塑料管道系统——聚乙烯(PE). [10] ASTM D2513:聚乙烯(PE)燃气压力管材,管道组件和管件的标准规格. [11] ISO 4433: 热塑性塑料管材.耐液体化学品. [12] ISO 1167-1: 用以输送流体的热塑性塑料管材,配件和附件——耐内压力性的测定. [13] A. Frank, W. Freimann, G. Pinter, R. W. Lang, Eng Fract Mech, 2009, 76, 2780. [14] P.F. Schoeffl,R.W. Lang,S. Liedauer,APST 3 会议,2013,林茨/奥地利. [15] P.F. Schoeffl,R.W. Lang,油田相关的液体媒介对PE100级管道材料的慢速裂纹增长行为的影响,文章即将发表. [16] G. Dörner,R. W. Lang,聚合物降解与稳定,1998,62,421. [17] G. Dörner,R. W. Lang,聚合物降解与稳定,1998,62,431. [18] P.F. Schoeffl,R.W. Lang,G. Zehethofer,塑料管道 XVI. 会议,2012,巴塞罗那/西班牙.
(翻译:福建纳川管材科技股份有限公司 魏作友 徐平来; 校对:国家建筑材料工业建筑围护材料及管道产品质量监督检验测试中心 李延军)
|